In India’s fast-paced world of ecommerce, logistics operations have become more vital than ever in resolving the efficiency of supply chains. In 2024 alone, the Indian logistics market was valued at over $317.26 billion, growing at a rate of 8.8% annually. With India becoming a global hub for e-commerce and manufacturing, the demand for seamless logistics operations has surged. Companies are shifting from traditional methods to more integrated, tech-driven logistics and warehousing solutions. But what do logistics operations really entail? How do they impact different sectors, such as B2B and D2C businesses? Let’s break it down.
What are Logistics Operations?
Logistics operations involve planning, implementing, and controlling the efficient, cost-effective flow of goods, services, and information. This includes everything from warehousing services, inventory management, transport services, last-mile delivery, and returns management. Logistics operations are the backbone of any supply chain, ensuring that products move smoothly from factories to end consumers.
In India, where the geographical spread and infrastructure challenges are significant, logistics operations play a key role. The complexity is even more prominent in the context of ecommerce fulfillment, manufacturing, and retail, where businesses have to juggle multiple deliveries, vast distances, and high consumer expectations.
Importance of Logistics Operations
Importance in B2B Businesses
Regarding B2B logistics, businesses depend heavily on the seamless movement of large volumes of goods. In B2B environments, logistics operations make sure that companies can meet their production schedules without delays, which can be essential for industries like manufacturing and automotive. For instance, poor logistics management could result in missed production deadlines, leading to massive financial losses. Efficient B2B logistics operations, on the other hand, enhance productivity, reduce lead times, and optimize the supply chain from procurement to final delivery.
Importance in D2C/Retail Businesses
Logistics operations are even more dynamic for retail warehousing and direct-to-consumer (D2C) businesses. These businesses require a fast, flexible, and consumer-centric approach from logistics companies. With the rise of e-commerce giants and the expectations of same-day or next-day deliveries, retail warehousing partners have evolved. The efficiency of logistics operations directly impacts customer satisfaction in D2C businesses. For example, delays in last-mile delivery or poor inventory management can result in lost sales and brand credibility.
5 Major Key Functions of Logistics Operations
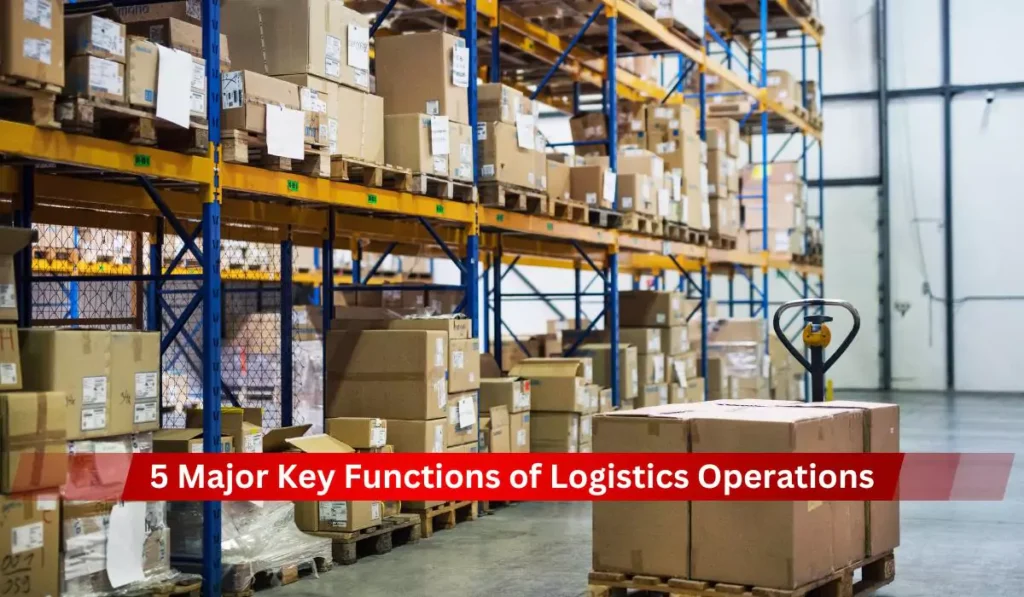
1. Transportation Management
Transportation management is the main function of logistics operations. The Transportation process involves the movement of goods from one location to another using different methods, such as road, rail, sea, and air. An effective transportation process guarantees that companies’ goods reach their destinations securely, on time, and in good condition. Efficient Transportation is important for B2B and D2C businesses.
2. Warehousing and Inventory Management
Warehousing and inventory management are crucial for securely storing clients’ products and accurately managing stock levels. A well-organized warehouse operation ensures that clients’ inventory is easy to locate, reducing lead times and improving order fulfillment. Inventory management also helps businesses prevent stockouts and overstock situations, leading to better cash flow.
3. Order Fulfillment
The fulfillment process ensures that customer orders are processed, picked, packed, and shipped in a timely and correct manner. This process is essential in D2C and B2B businesses, where quick deliveries are often a key selling point. Many warehousing companies now use modern technology to make their order fulfillment process faster and more efficient.
4. Last-Mile Delivery
Last-mile delivery refers to the final step in the delivery process, where the product is delivered to the consumer. This is the most expensive and complex part of logistics operations, especially in urban areas where traffic and infrastructure challenges can lead to delays in product deliveries. Last-mile delivery usually accounts for 53% of total shipment costs.
5. Reverse Logistics
Reverse logistics, also called returns management, handles returns and exchanges of products. Returns management makes sure that returned products are efficiently collected, inspected, and shipped another product to the customer or refunded as per the client’s return policy. Effective reverse logistics can minimize warehousing costs and improve customer satisfaction.
How to Optimize Your Operations and Logistics – Best Practices
Optimizing logistics operations is necessary for businesses to stay competitive in this growing market. Here are a few best practices that help companies to optimize their logistics operations:
- Leverage Technology—Implementing technology such as warehouse management systems (WMS), transportation management systems (TMS), and inventory tracking systems can automate processes and reduce errors. Make sure to utilize the latest technology to make your logistics operation more secure and quick.
- Data-Driven Decision Making—Data is the most powerful thing in inefficient logistics. Always Analyze logistics data, such as delivery times, order accuracy, return products, and transportation costs. This process will help businesses identify inefficiencies and areas for improvement.
- Collaborative Planning—Collaborating with suppliers, vendors, and logistics service providers can improve demand forecasting and inventory planning, reducing stockouts and excess inventory.
- Sustainability—Businesses should focus on eco-friendly practices, such as optimizing routes for fuel efficiency, using electric vehicles for deliveries, and using solar panels for electricity to reduce carbon footprints and appeal to environmentally conscious consumers.
Challenges and Solutions Ecommerce Companies Face in Logistics Operations
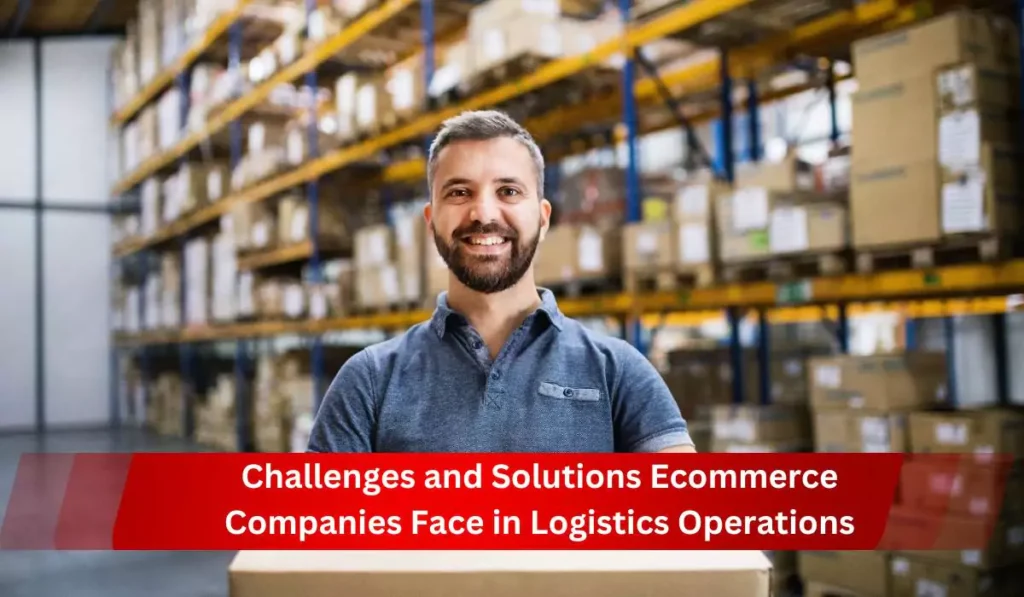
Ecommerce businesses face multiple challenges in logistics operations, particularly in extensive and diverse markets like India. From last-mile delivery complexities to handling high return rates, companies need to overcome these challenges to ensure smooth operations. Let’s explore some of the key challenges and potential solutions.
Infrastructure Limitations
India’s logistics network is still evolving, and infrastructure limitations can significantly slow down delivery timelines. Many rural areas face challenges with unreliable roadways and insufficient logistics hubs, which make it difficult to fulfill timely orders in remote areas.
Solutions:
To overcome infrastructure challenges, businesses need to adopt multi-modal transport systems that combine different modes of Transportation (e.g., road, rail, and air) to minimize delays and improve efficiency. Partnering with local courier services because they understand regional difficulties; also, they ensure faster, more reliable deliveries. Additionally, ecommerce companies and B2B portals in India can invest in hyperlocal delivery warehousing. Companies can set up smaller fulfillment centers in India’s key urban areas to provide faster shipments and better service to rural areas.
High Cost of Last-Mile Delivery
Last-mile delivery is one of the most expensive elements of logistics, especially in densely populated or traffic-heavy cities like Delhi, Mumbai, and Bangalore. In fact, last-mile delivery can account for up to 53% of a company’s total logistics cost, now you know the importance of last-mile delivery. The major challenge in last-mile delivery is to maintain the balance of delivery speed and cost-effectiveness, as customers demand faster deliveries without increasing prices.
Solutions:
Ecommerce companies are using more and more technology and innovation-driven operations to cut down the high cost of last-mile delivery. Here are some basic solutions to optimize the last-mile delivery cost without hampering the delivery time:
- Implement route optimization software, which uses algorithms to find the shortest and traffic-free delivery routes, which saves fuel and time.
- Build and Partner with local delivery hubs or micro-fulfillment centers because they reduce the distance between the fulfillment point and the customer. That helps companies to lower transportation costs and improve delivery times.
- Experimenting with autonomous vehicles and drone deliveries can provide long-term savings, especially in urban areas with traffic congestion.
Reverse Logistics and High Return Rates
Ecommerce businesses are booming and growing rapidly in India, and return rates are also increasing. If we analyze the data, return rates in the fashion and electronics sectors can go as high as 30%. The return rate is much higher in the peak and festive seasons. Managing returned products is a complex process. It involves collecting the products, inspecting them, and restocking returned products, which adds to operational costs and can lead to inventory disruptions.
Solutions:
Ecommerce companies can simplify their return process by automating them. Companies need to Offer easy-to-use return portals for customers that simplify the return process and make it more efficient. Also, businesses can implement smart return management systems to analyze return data, which helps them identify common reasons for returns and take proactive actions to reduce returns.
For example, more detailed product descriptions and accurate sizing guides can lower return rates in the fashion industry. Businesses can reduce the complexity and cost of handling returns by partnering with 3PL providers.
Managing Peak Demand and Seasonal Fluctuations
Everyone is aware of Big Billion Day, Great Indian festival sales, and festival sales like Diwali and Christmas. These types of sales lead to Peak Demand in ecommerce platforms. If companies do not prepare their logistics operations according to peak seasons, that can lead to bottlenecks, inventory shortages, and late deliveries. The major challenge is predicting the right stock levels and delivery capacity.
Solutions:
Scalable logistics is one of the solutions used to tackle peak demand. Flexible warehousing solutions, such as on-demand or shared warehousing, allow companies to expand their storage capacity during high-demand and peak seasons. Data analytics and demand forecasting help to optimize inventory levels and prevent stockouts based on historical trends. Partnering with third-party logistics companies that have the infrastructure to handle sudden spikes in volume.
Compliance and Regulatory Challenges
Logistics operations usually have to comply with different regulations. Tax laws, environmental guidelines, certification, and safety standards are some of them. In India, Goods and Services Tax (GST), road and traffic law, and other regulatory changes have a significant impact on logistics operations. International deliveries are more complex because they need customs clearance. Navigating these complex regulations can be a challenge, especially for small and medium ecommerce companies.
Solutions:
Companies can adopt regulatory management software that tracks and updates compliance requirements in real time. Outsourcing legal advisers or consultants who specialize in logistics also helps them comply fully with evolving rules. For international shipments, companies can adopt customs management tools. These tools can help them automate compliance checks and reduce the risk of delays at international borders. Businesses can also outsource custom bonded warehouses for cross-border deliveries.
Inventory Management and Stock Visibility
Effective inventory management is the key to success for ecommerce companies. Maintaining stock levels across multiple sales channels and warehouses takes time and extra effort. If companies can’t do proper inventory management, that can lead them to stockouts, excess inventory, and dissatisfied customers. Even companies can lose their sales if they don’t manage their inventory properly.
Solutions:
Inventory management systems (IMS) or warehouse management systems (WMS) are the most common software used for managing inventory and providing real-time updates on stock levels across all warehouses and sales channels. Warehouse and inventory management systems have an inbuilt auto alert feature for low stock levels, which helps businesses refill their inventory before stockouts. Businesses can also adapt demand forecasting tools that predict stock requirements more accurately based on historical sales data. This practice minimizes both stockouts and overstock.
Maintaining Consistent Customer Experience Across Channels
Companies whose products are on multiple ecommerce platforms, as well as in-store, could find it challenging to manage logistics to ensure consistent service across multiple sales channels, especially when coordinating deliveries, inventory, and returns. Handling all sales channels at a time can be challenging.
Solutions:
Adoption of an omnichannel logistics strategy can maintain a consistent customer experience for ecommerce businesses. Omnichannel logistics strategy involves integrating inventory and order management systems across all channels so customers receive a suitable experience regardless of where they shop. Implementing click-and-collect options or buy-online-pick-up-in-store (BOPIS) can also offer flexibility to customers. That leads to reducing last-mile delivery costs along with enhancing the customer experience. Adopt the centralized customer service platforms that track interactions across channels, ensuring that any issues are resolved instantly, further improving customer satisfaction.
Ensuring Sustainability in Logistics
As environmental concerns rise, consumers and businesses alike are demanding more sustainable logistics operations. The major challenge is reducing carbon footprints while maintaining operational efficiency. Eco-friendly logistics solutions often come with higher upfront costs that make it difficult for small businesses to adopt them.
Solutions:
Companies can implement sustainable practices by optimizing delivery routes that reduce fuel consumption. Switching to electric vehicles (EVs) for last-mile deliveries is one more good option for sustainable practices. As well as, companies can adopt eco-friendly packaging materials, reducing plastic use and waste. Carbon offset programs can help businesses counterbalance their environmental impact by investing in green initiatives.
Although the costs of all these practices may be higher, these initiatives contribute to sustainability, improve brand reputation, and appeal to environmentally conscious consumers.
Technological Innovations in Logistics Operations
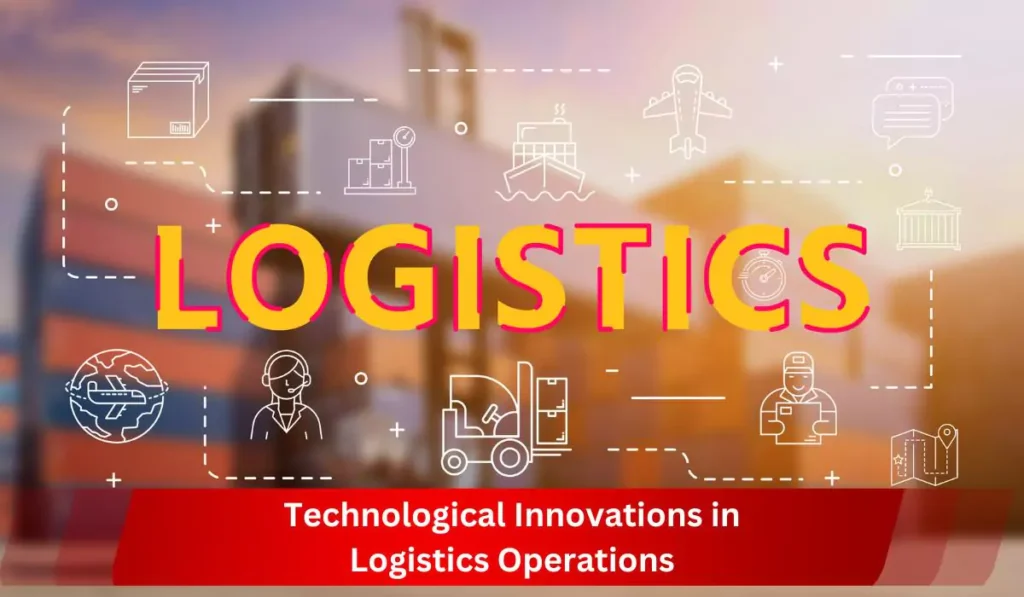
Technology is revolutionizing logistics operations in 2024. Let’s discuss some key innovations:
- Artificial Intelligence (AI) – AI helps find the best routes for delivery, predict demand, and manage inventory more efficiently. AI-based systems can automate everyday tasks that allow businesses to focus on more strategic areas.
- Blockchain – Blockchain technology makes sure transparency and traceability in logistics operations. It helps verify the authenticity of products and creates tamper-proof records of goods moving through the supply chain.
- Internet of Things (IoT) – IoT-enabled devices such as smart sensors and GPS trackers allow businesses to track shipments in real-time. These things reduce the risk of theft, damage, and delays, ensuring better accountability.
- Autonomous Vehicles and Drones – Autonomous delivery vehicles and drones make last-mile deliveries faster and more cost-effective. These innovations are particularly useful in overcrowded urban areas where traditional delivery vehicles struggle.
Future Trends in Logistics Operations
As we move into the future, several trends are set to shape logistics operations:
- Sustainability – The demand for eco-friendly logistics practices has increased. Logistics companies in India will continue to adopt sustainable packaging, use electric vehicles, and implement carbon-neutral transportation options.
- Hyperlocal Warehousing – Businesses are increasingly setting up small, strategically located warehouse for ecommerce in urban centers to shorten delivery times. This trend, known as hyperlocal warehousing, improves last-mile efficiency.
- Robotic Process Automation (RPA) – Robotic process automation is used to automate routine tasks in logistics, such as data entry and inventory counting. This reduces human error and increases operational efficiency.
- Omni-channel Fulfillment – Consumers now shop across multiple channels, from websites to physical stores. Omni-channel fulfillment integrates logistics operations across all channels that make sure a seamless customer experience regardless of the platform.
Conclusion
Logistics operations are the lifeline of any business in 2024, particularly in the context of India’s rapidly growing e-commerce and retail sectors. From optimizing last-mile delivery and leveraging cutting-edge technology, warehousing and logistics companies must stay agile and innovative to succeed. As the landscape evolves with new challenges and opportunities, businesses that prioritize efficiency and customer satisfaction through well-optimized logistics operations will stay ahead of the competition.