If your business involves storing products, it’s important to understand warehousing costs. Knowing these costs can help you manage your business better. Warehousing costs can significantly impact your profits. Understanding these warehouse costs can help you make smarter financial choices.
Companies who are looking for warehousing services, it’s difficult to consider factors like location, storage requirements, and handling fees. For instance, in Indian metro cities, the average cost of warehousing can range from INR ₹35 to INR ₹100 per square foot annually, depending on the location and facilities offered. Whether you’re new to the world of warehousing or looking to optimize your current operations, this guide will provide you with the insights needed to navigate these expenses effectively. Let’s dive in and explore how you can manage and reduce warehousing costs to boost your business’s efficiency and profitability.
What are Warehouse costs?
Warehouse costs are all those expenses that arise when maintaining business stocks in the company’s warehouse. That is, all those that allow a warehouse to be kept in operation and to protect and manage the stock.
Types of Warehouse costs
Warehouse costs can be of different types and are divided between fixed costs and variable costs. The latter are those that increase or decrease depending on the products that are kept in stock.
To optimize warehousing costs, it is essential to have an intuitive, customizable and complete warehouse management system, like the one we offer you at AAJ Supply Chain Management. With the help of such a warehouse solution, the entire process is simplified and streamlined, among many other advantages. Here are the 2 main elements that affect Warehousing Costs:
Fixed costs
- Rental or purchase of space: The location and size of the warehouse are determining factors in this expense.
- Maintenance costs: Includes cleaning, security, repairs and warehouse supplies.
- Personnel costs: Salaries and benefits of employees who work in the warehouse.
- Equipment costs: Depreciation and maintenance of equipment such as forklifts, shelving, and inventory management systems.
Variable costs
- Inventory costs: Value of stored products, including financing and obsolescence.
- Handling costs: Product movements within the warehouse and logistics (picking, packing, loading/unloading).
- Order management costs Order processing, inventory management and customer service.
Below, We Explain What the Main Warehouse Costs are and What They Consist of:
1. Infrastructure costs
These are all those costs related to the infrastructure of the warehouse itself, from the rental or ownership of the place to the necessary financing, the maintenance or repair of the warehouse, the relevant taxes, insurance, etc.
2. Facility costs
These Warehouse costs include all those expenses related to maximizing Warehouse capacity and optimizing the existing loads inside. Such as, for example, forklifts, picking assistance devices, automatic packaging, Warehouse systems and, of course, warehouse management software.
3. Management and handling costs
These are all those Warehouse costs that allow the warehouse and its flow of materials to be kept active, such as the cost of personnel, the cost of technical equipment, its amortization and financing, supplies (such as energy or water), and packaging.
4. Stock maintenance costs
These are essential for Warehouse management strategies to give the expected results. Within this type of Warehouse costs, there are two subgroups:
- On the one hand, the cost of the stock itself.
- And, on the other hand, the cost of insurance will depend on the type of merchandise that is stored.
5. Other costs
This category includes all costs related to incidents or unforeseen events typical of Warehouse activity. Some examples are stockouts, possible damage to merchandise or inventory imbalances.
13 Factors That Affect Warehousing Cost in India
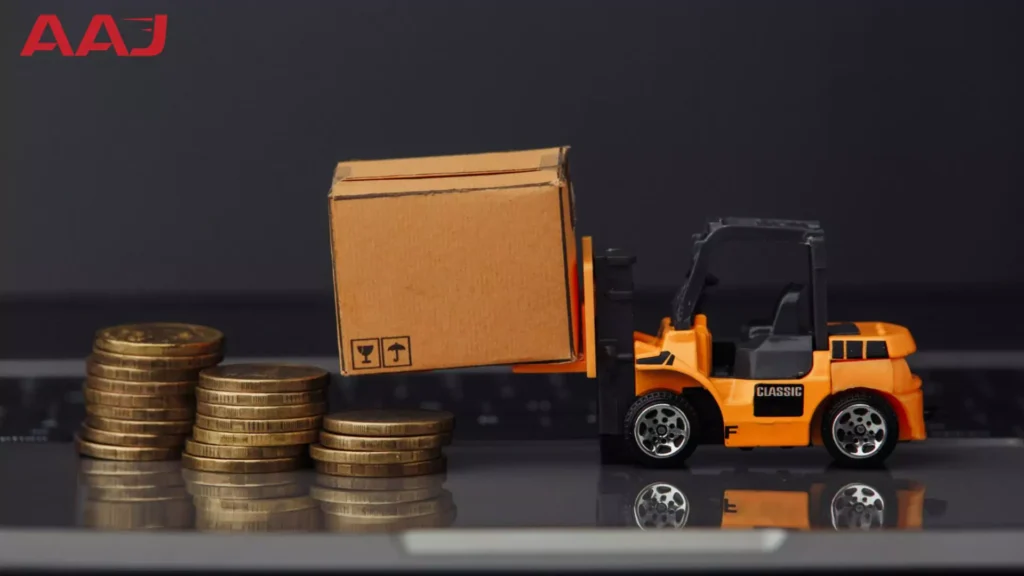
Location:
The location of a warehouse is a fundamental factor influencing its cost. Warehouses situated in prime locations, such as major cities or industrial zones, tend to have higher rental and operational expenses compared to those in rural areas. For example, a warehouse in Delhi or Mumbai may command a higher rental rate due to high demand and proximity to transportation hubs. In contrast, a warehouse in a less urbanized area like Sonipat, Jaipur or Coimbatore might offer cost savings but may have limitations in terms of accessibility.
Size of the Warehouse:
The size of the warehouse directly impacts Warehousing costs. Larger warehouses typically have higher rent and operational expenses but may offer economies of scale for storing larger quantities of goods. Conversely, smaller warehouses may be more cost-effective for businesses with limited warehouse storage needs but may lack the capacity for large-scale operations.
Type of Storage:
The type of warehouse required also affects warehousing costs. Temperature-controlled storage facilities for perishable goods or sensitive materials come with higher operational expenses due to specialized equipment and energy requirements. On the other hand, standard storage facilities for non-perishable goods are generally more affordable but still vary based on factors like security features and space utilization.
Duration of Storage:
How long consumer goods are stored in a warehouse also affects the warehouse cost. Long-term storage may offer discounts or lower rates per unit of time, whereas short-term or seasonal storage may incur higher costs. Businesses need to optimize their storage duration to balance cost efficiency with inventory management needs.
Employee Costs:
Employee costs, including wages, benefits, and training, contribute significantly to warehousing expenses. Skilled labor for tasks such as inventory management, order picking, and equipment maintenance may command higher wages, adding to operational costs. Additionally, fluctuations in employee market conditions and regulatory changes can impact employee costs over time.
Utilities:
Utilities encompass a range of expenses, including electricity, water, petrol pricing, gas, and waste management. These costs vary based on factors like warehouse size, equipment usage, and environmental regulations. For example, a warehouse with energy-efficient lighting and heating systems may reduce electricity costs, while effective waste management practices can minimize disposal expenses.
Security Measures:
Investing in robust security measures, such as surveillance systems, access controls, and security personnel, is essential to protect valuable inventory and assets. However, these security measures contribute to warehousing costs, particularly in high-risk areas or industries prone to theft or damage.
Insurance:
Insurance coverage for warehouses, including property insurance, liability insurance, and cargo insurance, is important to mitigate risks associated with theft, accidents, or natural disasters. The cost of insurance premiums depends on factors like coverage limits, deductibles, and the overall risk profile of the warehouse and its contents.
Technology and Automation:
More than 80% of the world’s warehouses still do not use any type of automation in their operations. In the last decade, only 5% of warehouses have adopted automation. Implementing technology and automation solutions, like inventory management software, RFID tracking systems, and automated material handling equipment, can enhance efficiency and productivity in warehousing operations. While these technologies offer long-term cost savings through improved accuracy and reduced labor requirements, initial investments and maintenance costs must be considered.
Handling and Packaging:
Costs related to handling and packaging, including materials, equipment, and labor, impact overall warehousing expenses. Efficient handling practices and optimized packaging designs can minimize waste and reduce costs, while specialized handling requirements for fragile or hazardous goods may incur additional expenses.
Transportation Links:
The proximity of warehouses to transportation links, such as highways, ports, and railroads, influences transportation costs and logistics efficiency. Warehouses located near major transportation hubs benefit from lower shipping and logistics costs and faster door to door delivery times, contributing to overall cost savings for businesses.
Lease Agreements and Terms:
The terms of lease agreements, including rental rates, lease duration, renewal options, and clauses for maintenance and repairs, affect warehousing costs. Negotiating favorable lease terms and understanding contractual obligations can help businesses manage costs and avoid unexpected expenses.
Inventory Management Systems:
Effective inventory management systems and practices, such as real-time tracking, demand forecasting, and stock optimization, are important for minimizing warehouse storage costs and avoiding inventory-related expenses like overstocking or stockouts. Investing in advanced inventory management technologies can lead to cost efficiencies and improved order fulfillment and customer satisfaction.
6 Tips to Optimize Your Warehousing Costs
As businesses grow, warehousing becomes a crucial component of the supply chain. However, warehousing costs can quickly add up, impacting your profits. If you’re looking to optimize your warehousing expenses without compromising efficiency, here are some practical tips to consider.
1. Understanding Your Warehousing Needs
Before diving into cost-saving strategies, it’s essential to understand your specific warehousing needs. Are you storing perishable goods that require climate control, or do you need a simple storage space for non-perishable items? Knowing your requirements will help you choose the right warehouse and avoid paying for unnecessary features.
2. Choose the Right Location
Proximity to Suppliers and Customers
Selecting a warehouse in a strategic location can significantly reduce transportation costs. A warehouse closer to your suppliers and customers minimizes shipping distances, saving both time and money. For example, if your primary market is in southern India, a warehouse in Chennai or Bangalore warehouse, could be ideal.
Consider Local Regulations and Taxes
Different regions have varying tax rates and regulations. Research the local laws to find areas with favorable tax policies that can lower your overall expenses. For instance, some regions might offer tax incentives for businesses that set up warehousing operations.
3. Optimize Warehouse Space
Efficient Layout Design
An efficiently designed warehouse layout maximizes storage space and minimizes handling time. Use vertical space effectively by installing high shelves and racks. Implementing a smart layout can reduce the need for additional square footage, lowering your rental costs.
Regular Inventory Audits
Conduct regular inventory audits to ensure you’re not paying for space you’re not using. Overstocking can lead to unnecessary storage costs, while understocking can result in missed sales opportunities. Use inventory management software to keep track of stock levels and optimize your storage space.
4. Utilize Technology
Warehouse Management Systems (WMS)
Investing in a robust Warehouse Management System (WMS) can streamline your operations and reduce Warehouse costs. A WMS helps automate various tasks such as inventory tracking, order fulfillment, and shipping, reducing the need for manual Employees and minimizing errors.
Automated Storage and Retrieval Systems (AS/RS)
Automated systems can significantly improve efficiency and reduce Employee costs. AS/RS systems use robotics to store and retrieve items, speeding up the process and reducing the risk of damage or loss. While the initial investment might be high, the long-term savings can be substantial.
5. Negotiate Contracts Wisely
Flexible Leasing Options
Look for warehouse companies that offer flexible leasing options. Short-term leases or month-to-month agreements provide the flexibility to scale up or down based on your business needs. This way, you won’t be locked into a long-term contract that doesn’t suit your evolving requirements.
Volume Discounts
If you anticipate needing more space in the future, negotiate volume discounts with your warehouse provider. Committing to a larger space over time can often result in lower rates per square foot, leading to significant savings.
6. Outsource Non-Core Activities
Third-Party Logistics (3PL) Providers
Outsourcing warehousing and logistics to a third-party logistics service provider can be cost-effective. 3PL Logistics Companies offer comprehensive services, including storage, transportation, and inventory management. They benefit from economies of scale, allowing you to take advantage of lower costs than managing these functions in-house.
Focus on Core Competencies
By outsourcing warehousing, you can focus on your core business activities. That not only saves money but also improves efficiency and allows you to allocate resources more effectively.
Conclusion
Efficient management of Warehouse costs is an investment in the future of your company. Working with AAJ Supply Chain Management can be your strategic ally to optimize Warehousing costs. Contact us and discover how we can help you achieve your objectives and goals.