Inventory storage refers to the systematic organization of goods and products inside the warehouse to enhance order fulfillment. It even prevents overstocking problems and improves supply chain efficiency. You can adopt various technologies like RFID, automated storage and retrieval systems, or adopt FIFO and JIT management techniques to have efficient inventory storage inside the warehouse and drive business growth and profitability. Let’s deep dive into inventory storage and understand its role in the supply chain and warehouse, its benefits, & Challenges.
Understanding Inventory Storage

Inventory storage refers to storing raw materials, semi finished goods, or finished goods on the warehouse shelf or racks that are ready for sale or production. A well-structured inventory storage system keeps goods secure and ready to meet customer demand. It also includes barcoding and tracking for efficient management.
Warehouse management systems can track these products in real time and avoid problems like overstocking or out-of-stock issues. Inventory storage is essential for efficient supply chain operations in various industries like retail, e-commerce, and many more.
General Storage Vs. Inventory Storage
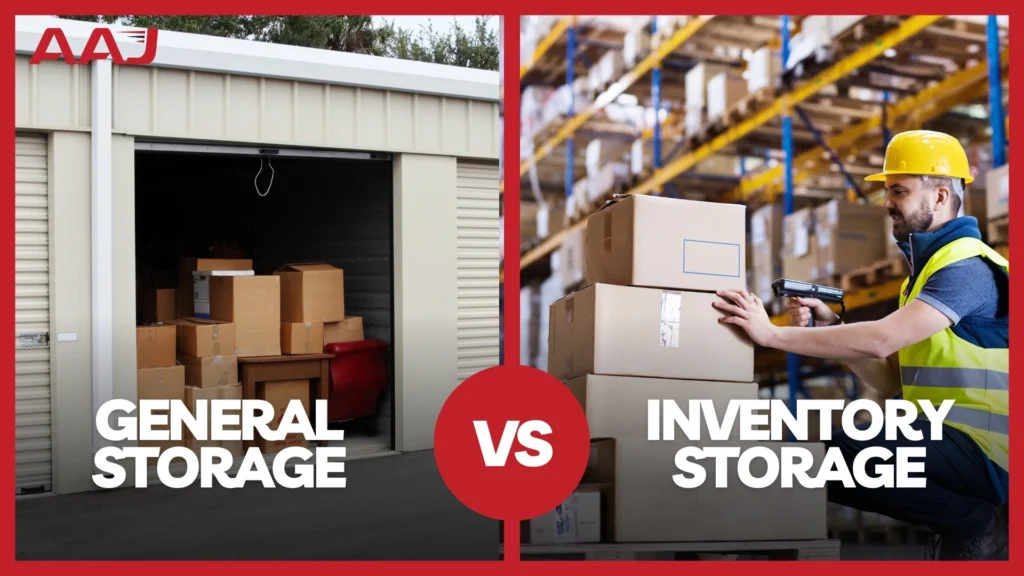
General storage refers to the storage of various products, office supplies, or documents without focusing on inventory management. There is no requirement for systemic storage, and products do not even have a specific tracking number. General storage is used for personal or office use.
However, Inventory storage requires proper management and organization. It involves systematic storage where each product is assigned a tracking number or SKU (Stock Keeping Unit) for easy identification. Inventory storage is essential for businesses that need to monitor stock levels, track product movement, and ensure timely restocking.
Inventory storage follows a structured approach, with proper shelving, labelling, and constant digital tracking through warehouse management systems (WMS). It is commonly used in retail, e-commerce, and supply chain operations to maintain accuracy and efficiency.
Role of inventory storage in supply chain and warehouse management
Inventory storage is important for supply chain and warehouse management.
For example, systematic inventory storage improves the warehouse layout and storage techniques. It frees up space to store other goods and products on shelves and racks. Proper inventory storage even speeds up order fulfillment and improves a business’s profit.
Types Of Inventory Storage Methods
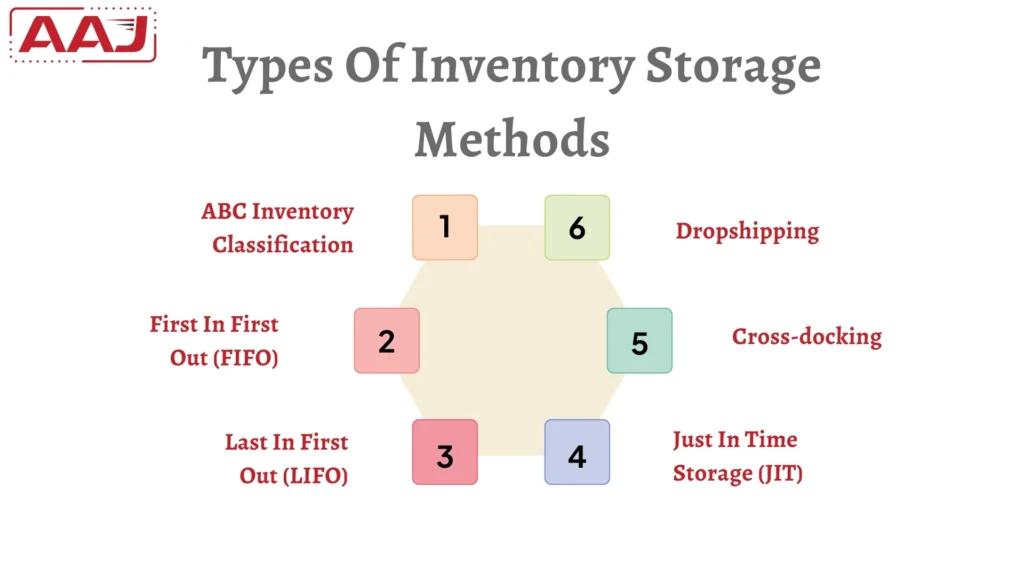
There are various inventory storage methods, and each one has its pros and cons. Let’s discuss it in detail:
1. ABC Inventory Classification
The ABC inventory classification method divides inventory into three groups. A Class indicates that inventories are of very high value and require frequent monitoring. Class B indicates that inventories are of moderate value and require regular monitoring. Class C indicates that inventories are of low value and require minimal attention.
2. First In First Out (FIFO)
The oldest inventories are sold out first in and first out. This model is best for perishable or time-sensitive goods, as they are sold out first before new stock is consumed. The FIFO model has various benefits, like reducing product spoilage in the warehouse.
3. Last In First Out (LIFO)
Here, the most recently added inventories are sold out first. This method is best for businesses dealing with bulk raw materials or nonperishable goods. With this model, businesses save taxes during inflation.
4. Just In Time Storage (JIT)
The just-in-time storage method ensures that inventory is ordered and stored when required. This model’s main goal is to reduce wastage and increase the efficiency of supply chain operations.
JIT does long-term contracts and good collaboration with reliable suppliers so that they can supply the raw materials exactly when required.
5. Cross-docking
Cross-docking is a method in which products spend as little time as possible in the warehouse storage. First, the products are shipped to the warehouse and then unloaded to one side of the dock. They are sorted and then immediately loaded on another truck to reach their final destination.
6. Dropshipping
Dropshipping is an inventory model in which the manufacturer bears the shipping burden. Manufacturers send the products directly to the customer without storing them in warehouses.
Both drop shipping and cross-docking eliminate the need for large storage areas and do faster order fulfillment.
Inventory Storage Racks: Choosing The Right System
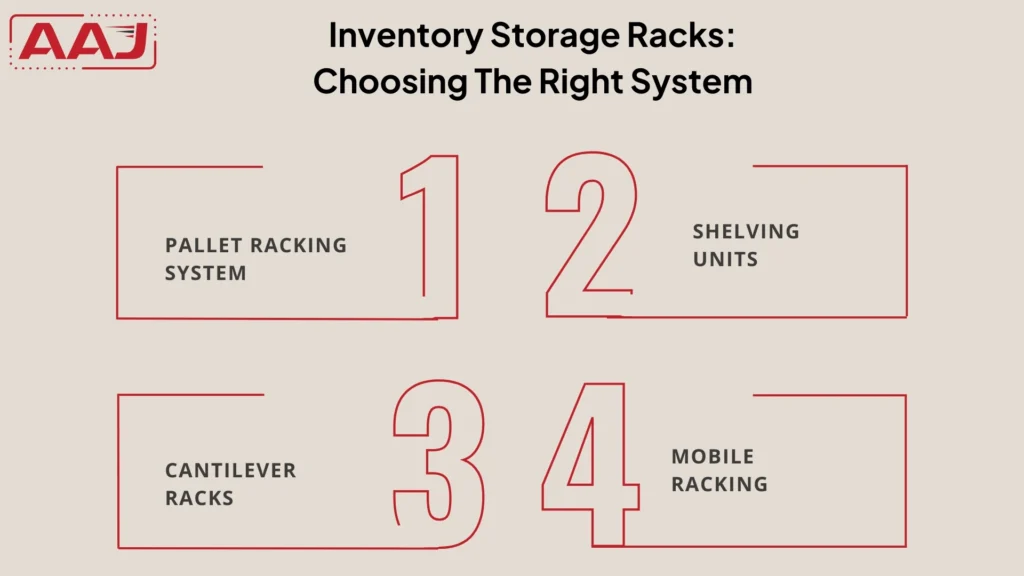
1. Pallet Racking System
A racking system is made up of various modules with shelves and is used for storing goods and products. It allows better tracking of goods for order fulfillment.
There are various types of racking systems, but the most common and popular one is the pallet racking system. It improves warehouse organization by better-using space. Simultaneously, it increases safety inside the logistics warehouse space.
Here, the goods on pallets are placed on vertical steel framework racks by forklift machines. So, in this storage system, there are three basic elements: pallets, racks, and forklifts. These three are chosen based on the product to be handled, storage requirements and many other factors. The warehouse staff arranges the palletized goods on the racks in two ways: direct access and compacting.
Direct access can be accessed directly and individually. It does not require the movement of other pallets. Hence, this type of arrangement reduces handling time.
However, in compact storage, the pallets are densely packed. You need to move pallets to access the deeper ones.
2. Shelving Units For Different Inventory Types
Shelving units are meant to store different types of inventory in the warehouse. They are ideal for non-palletized inventories like retail products. They are of various types.
- Boltless shelving: They are simple to set up and adjustable. They do not have any bolts and are ideal for keeping small items.
- Wire Shelving: These shelving systems enhance the airflow and visibility of the products stored. Wire shelving is best for storing food supplies and electronics.
- Heavy-duty Shelving: Heavy-duty shelving is sturdy and consists of metal. They are ideal for storing bulk and heavy items.
3. Cantilever Racks For Long or Bulky Inventory
They are special storage systems meant to keep heavy and long inventories that will not fit on traditional pallet racks. The cantilever racks have robust vertical columns. Their horizontal arms are extended outward. They are open-faced, which allows seamless storage and removal of bulky items.
Cantilever racks are a great way to increase your warehouse’s storage capacity. They simplify the loading and unloading process and thus improve workflow efficiency in the warehouse. These racks are highly customizable and hence used in various industries, such as furniture, manufacturing, construction and many more.
Cantilever racks are made from high-gauge steel, so they are quite expensive compared to other racking options.
4. Mobile Racking for Space Optimization
The mobile racking system consists of two parts, i.e., racks and rails. The rails are built on the floor and can be moved either manually or electronically. You can move the racks backward or forward for loading and unloading of goods and products. Large storage areas benefit from having electronically controlled mobile racking systems.
Vertical Inventory Storage: Maximizing Space Efficiency
In the past, most warehouses depended on horizontal expansion to store goods. However, this approach was not possible because of the rise in real estate costs and limited horizontal space.
Vertical inventory storage means utilizing the vertical space of the warehouse for storing goods and products instead of horizontally. A business can use tall racks and shelves to stack inventory upwards.
Benefits Of Going Vertical In Inventory Storage
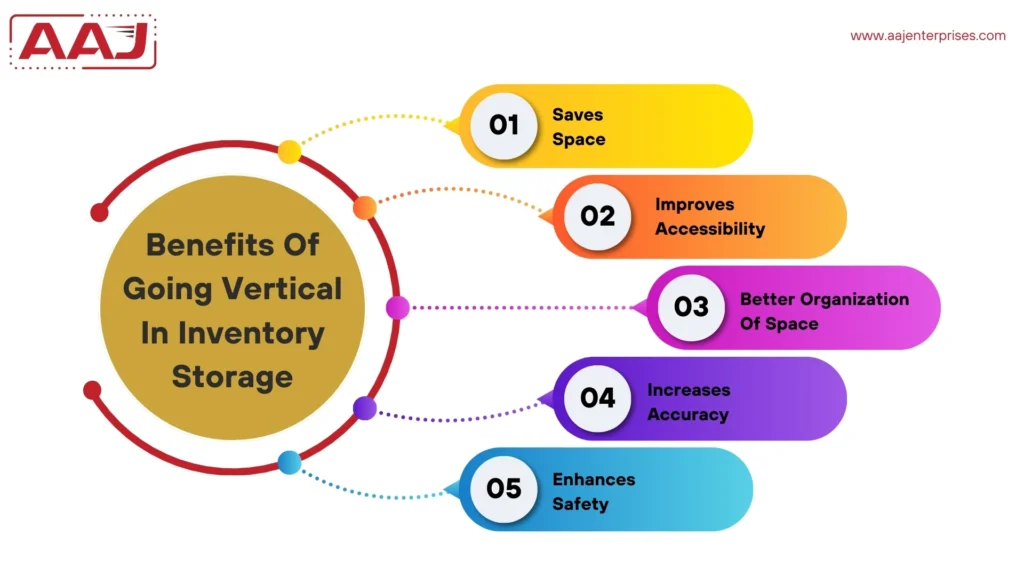
- Saves Space: A vertical storage system will utilize the vertical space properly and allow the warehouse to store more products efficiently.
- Improves Accessibility: A vertical carousel is an automated storage and retrieval system. It brings products directly to the operator, so the staff does not have to search for a particular product manually. This eliminates the warehouse staff’s picking time.
- Better Organization Of Space: Vertical warehouse storage solutions provide a structured and organized space inside the warehouse. The products are arranged systematically. This ensures that the warehouse staff can easily pick up the ordered product.
- Increases Accuracy: A vertical storage system properly integrates with an inventory storage system, which ensures proper product tracking. Proper inventory management in a vertical storage system avoids problems like stockouts and overstocking.
- Enhances Safety: A vertical storage system eliminates the need to bend or manually lift heavy objects in the warehouse, reducing the risk of injuries and improving safety.

Automated Storage and Retrieval System
It is a computer control system used to store and manage inventories in warehouses and distribution centers, reducing labour costs and increasing efficiency.
- The items are placed in their respective places inside the warehouse by robots, cranes or conveyors.
- The warehouse management system will record it and keep track of the stock levels.
Automated storage and retrieval systems have certain limitations, such as a high initial investment, which may not be possible for all enterprises. Again, they need regular maintenance to work efficiently, and you need to train your workers to handle the system.
Storage And Inventory Control: Best Practices
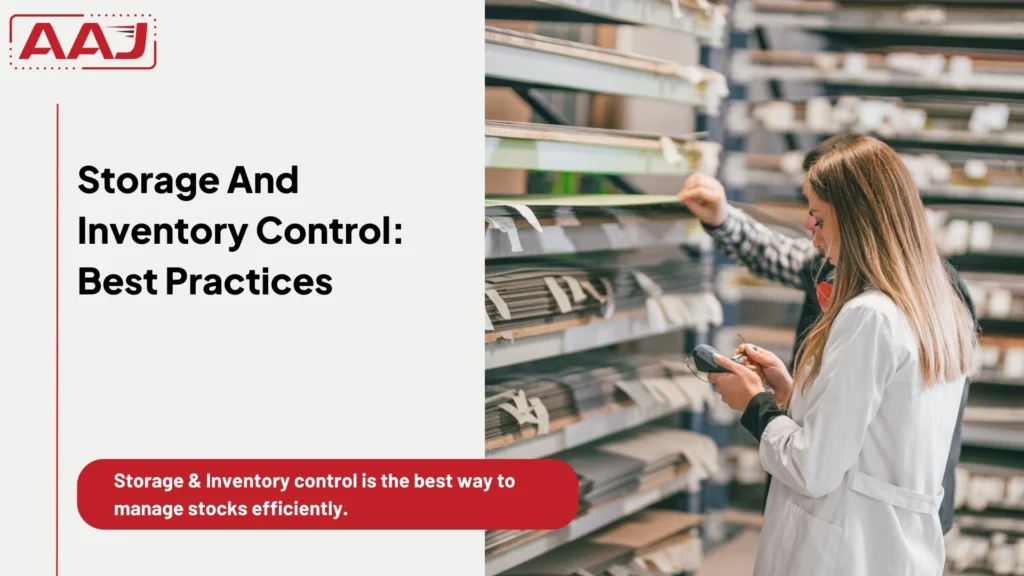
Inventory control is the best way to manage stocks efficiently. It avoids problems like overstocking and out-of-stock issues and ensures that products are available in the warehouse to meet customer demand.
Technology plays an important role in storage fulfillment center and inventory control. For example, let’s discuss barcodes. They are unique identifiers printed on the product label and are helpful in the quick identification of the product.
RFID(Radio frequency identification) tracks and identifies goods and products using radio waves. Thus, it enhances product visibility in a warehouse and eliminates the need to scan products manually, like barcoding. IoT integrates smart sensors and cloud computing to manage inventory in real-time.
Warehouse Inventory Storage: Optimizing Your Space
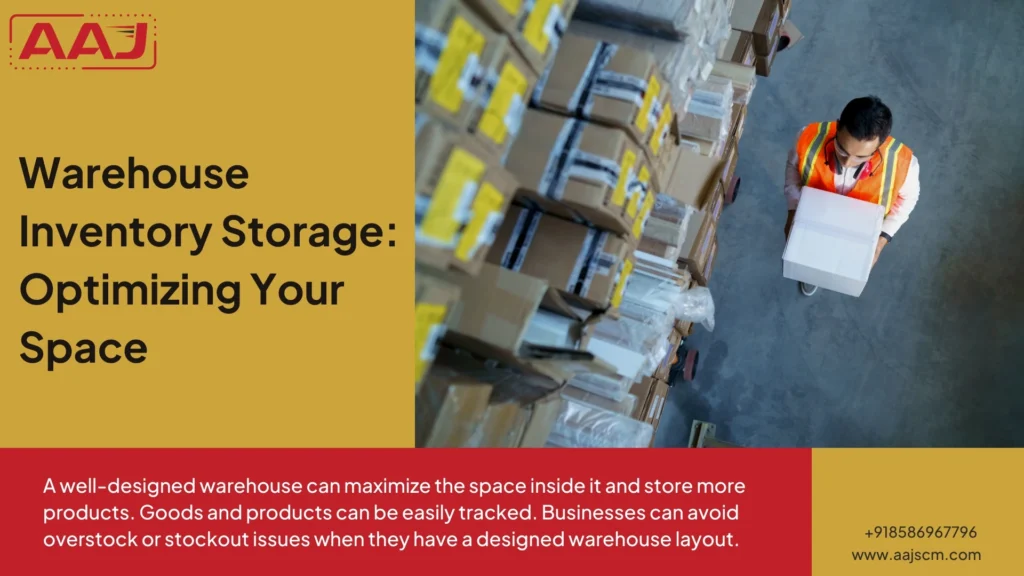
A well-designed warehouse can maximize the space inside it and store more products. Goods and products can be easily tracked. Businesses can avoid overstock or stockout issues when they have a designed warehouse layout.
Best Practices For Warehouse Layout Planning
- The efficient use of vertical storage can maximize the space inside the warehouse.
- You can use FIFO or LIFO inventory management techniques in the warehouse.
- Designate particular areas for receiving, packing and shipping in the warehouse.
- You should use a warehouse management system to track products effectively.
Importance Of Temperature-Controlled Storage
Temperature-sensitive goods like food and pharmaceuticals require climate-controlled storage to enhance their shelf life. You can install smart sensors to monitor temperature continuously. You should also separate zones for different temperature requirements.
For example, storing dairy products and vaccines requires temperature storage between 0 and 4 degrees Celsius. However, storing cosmetics and packaged goods requires a temperature between 15 to 25 degrees Celsius for proper storage.
Reducing Wasted Space With Smart Storage Planning
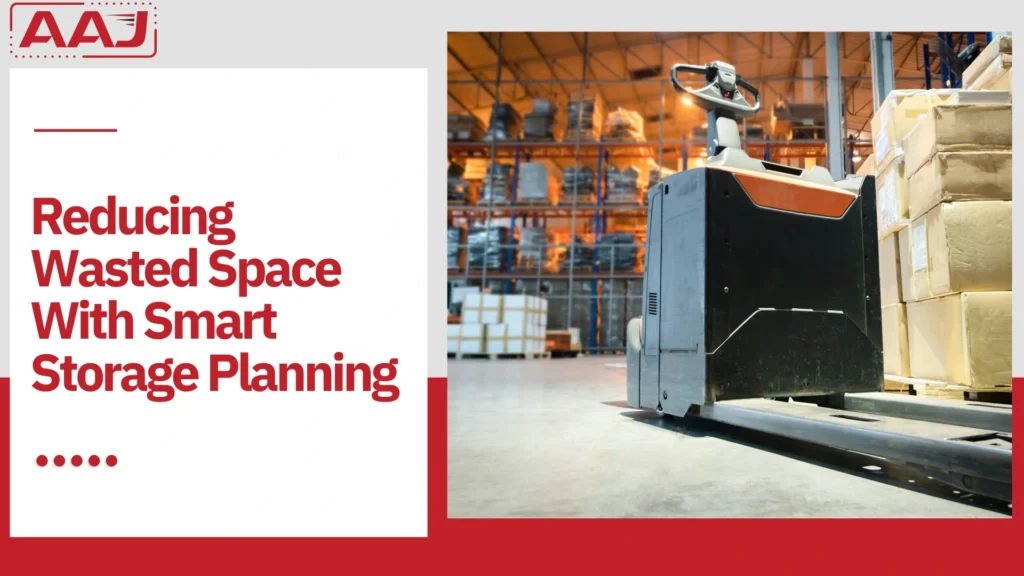
A few common factors waste warehouse space, as listed below.
- Overstocking
- Without the usage of vertical space.
- Inefficient picking path.
Below, we list a few strategies that can help make the best use of the warehouse space.
- Invest in mobile racking systems
- Use cross-docking to reduce the warehouse storage needs.
- Utilize vertical space in your warehouse.
Inventory Storage Costs: How To Minimize Expenses
Factors Affecting Inventory Storage Costs
Various factors affect inventory storage costs, Let’s see them:
- The larger the storage area in your warehouse, the higher the rental costs will be.
- The adoption of automated storage systems needs a high initial investment.
- Overstocking can increase the holding cost of the business.
- Manual handling of goods and products can increase labour expenses.
- Temperature-controlled storage increases the electricity consumption.
Cost-Effective Storage Solutions For Different Businesses
- You can implement drop shipping to reduce the storage needs of products,
- You can implement high-density storage solutions like mobile racking.
- You can adopt energy-efficient techniques to reduce electricity consumption.
- You can store products on on-demand warehousing.
Reducing Costs Through Automation And Lean Inventory Management
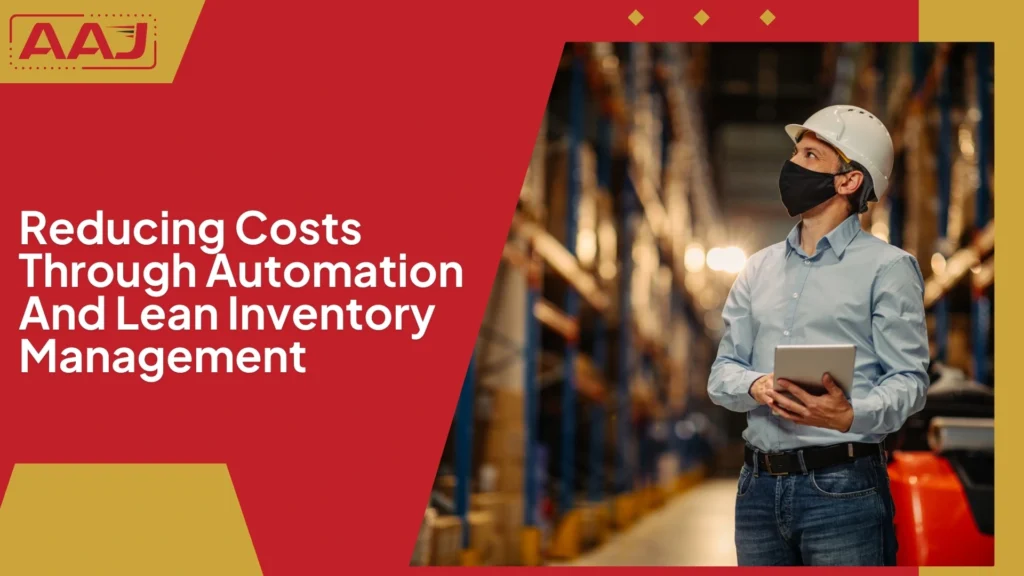
Warehouse automation can increase the efficiency of the picking and packaging warehousing operations. Simultaneously it decreases the labour costs of the business.
A business can even adopt lean inventory management strategies like ABC analysis and just-in-time inventory management.
Conclusion
Effective warehouse and inventory management is essential to reducing storage costs, increasing order fulfillment, and improving business productivity. There are various inventory storage strategies that you can adopt, like implementing vertical storage, adopting advanced technology like warehouse management systems and automation or adopting cross-docking. Warehouses can adopt energy-efficient warehouse solutions like solar-powered warehouses and green logistics to reduce carbon footprint in the atmosphere, and machine learning can even forecast product demand accurately and reduce stock inefficiencies.