Warehouse and inventory management have evolved significantly over the years, from manual stock-keeping to the current era of automation and data-driven warehousing solutions. Warehouse and inventory management are the backbone of supply chain operations. They ensure that goods are stored in the proper location and are available when required. Effective management can reduce warehouse storage costs, improve customer satisfaction and increase revenue for any business.
Let’s take a look at the history of warehousing management. Barcodes were invented in the 1970s, revolutionizing warehouse and inventory management. Scanners allowed for faster, more accurate data entry and reduced human error. By the 1980s, barcode technology became widely adopted in warehouses. Traditional inventory systems (like manual or spreadsheet-based) have an accuracy rate of 63%, while automated and WMS-driven warehouses achieve accuracy rates above 99%.
E-commerce accounts for around 45% of the total warehousing demand globally. The shift to online shopping has created an increased demand for real-time inventory visibility and efficient e commerce fulfillment operations.
An Overview About Warehouse And Inventory Management
Warehouse Management
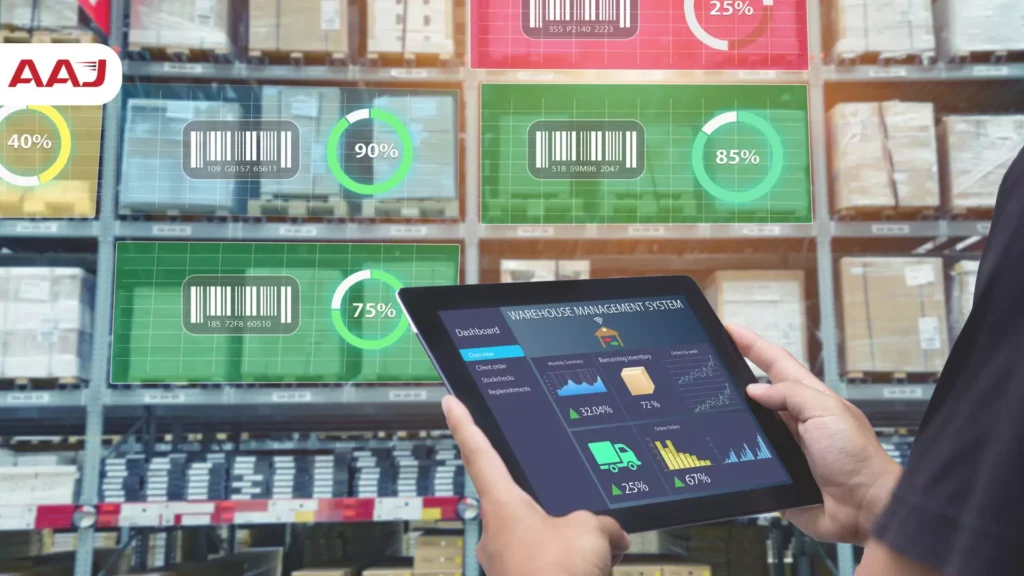
Warehouse management involves picking goods, arranging them in their proper place, and storing them. In the early 20th century, most warehouse operations were manual. Inventory records were kept on paper, making it difficult to track stock levels efficiently. Mistakes were common, and stock-taking was labor-intensive. Basic equipment like forklifts were used to transfer goods inside the warehouse.
The goods were maintained and sorted manually. However, that tends to cause various errors in product placement and counting. However, warehouse management systems are now dominated by digital systems. Everything is automated now. The warehouse management system automates various tasks like inventory tracking, shipping processes and many more. Nowadays, barcodes and multiple sensors are used to monitor the stocks inside the warehouse. Robots are even used in certain warehouses to pick up goods, store them, and arrange them. It reduces human work and speeds up operations.
Inventory Management
Inventory management means keeping track of the company goods or materials and ensuring that they are not overstocked or out of stock. Earlier inventory management was very tedious as it involved pen and paper methods and periodic counting of products. The Just-in-Time (JIT) strategy, introduced by Toyota in the 1970s, became popular in the 1980s. It emphasized reducing inventory holding costs by receiving goods only when needed, directly impacting warehousing operations. But now cloud-based systems are introduced which offer real-time visibility. It tracks stock levels, sales, and orders and reduces errors. Machine learning is used for optimizing inventory levels.
What Is Warehouse And Inventory Management?
Both warehouse and inventory management are important nodes of business supply chain operations. Let’s discuss them below.
1. Warehouse Management
Warehouse Management involves Various processes like:
- Receiving goods.
- Storing them.
- Picking goods on receiving a customer order.
- Packaging them properly inside the warehouse and then shipping.
Proper warehouse management will ensure that the goods are stored and managed properly so that they can be easy to access when receiving customer orders.
2. Inventory Management
Inventory means the goods that a company keeps in stock to meet customer demands and keeping track of how much is available and how much is required. It predicts future demands of products in the market and ensures the right amount of goods is available to fullfill the needs of the customer.
Type Of Warehouse And Inventory Management

Warehouse Management System Types
Choosing the right Warehouse Management System (WMS) can make or break your logistics game. So, what are the options? Let’s break it down.
1. Standalone Warehouse Management System
If you’re looking for a simple warehouse and Inventory management solution to handle core tasks like receiving goods, organizing inventory, packaging, and shipping, the Standalone WMS is your go-to partner. It’s a precise system that’s good for businesses looking to focus solely on their warehouse operations without needing to integrate with other platforms. Think of it as a dedicated manager solely handling your warehouse’s day-to-day actions.
2. Cloud Based Warehouse Management System
Need flexibility? A Cloud-Based WMS might be your best option to manage warehousing. You can access real-time data from any device, anywhere in the world. It’s perfect for businesses that want to scale, adapt, and keep their warehouse connected 24/7. No more waiting to get back to the office—just log in and manage your warehouse on the go.
3. Automated Warehouse Management System
For those who want to take automation to the next level, the Automated WMS is like having a team of robots running the show. From conveyor belts to robotic arms, this warehouse and Inventory management system automates the movement, storage, and retrieval of goods. It’s a game-changer for high-volume or B2B warehouses looking to boost efficiency and reduce manual labor.
4. Third-party Logistics Warehouse Management System
If outsourcing is more your style, a Third-party Logistics (3PL) WMS allows a third-party provider to manage the entire warehousing process. This option is ideal for businesses looking to focus on growth and leave warehousing operations in the hands of experts. It’s like having a professional logistics partner without the overhead costs of managing it in-house.
Types Of Inventory Management
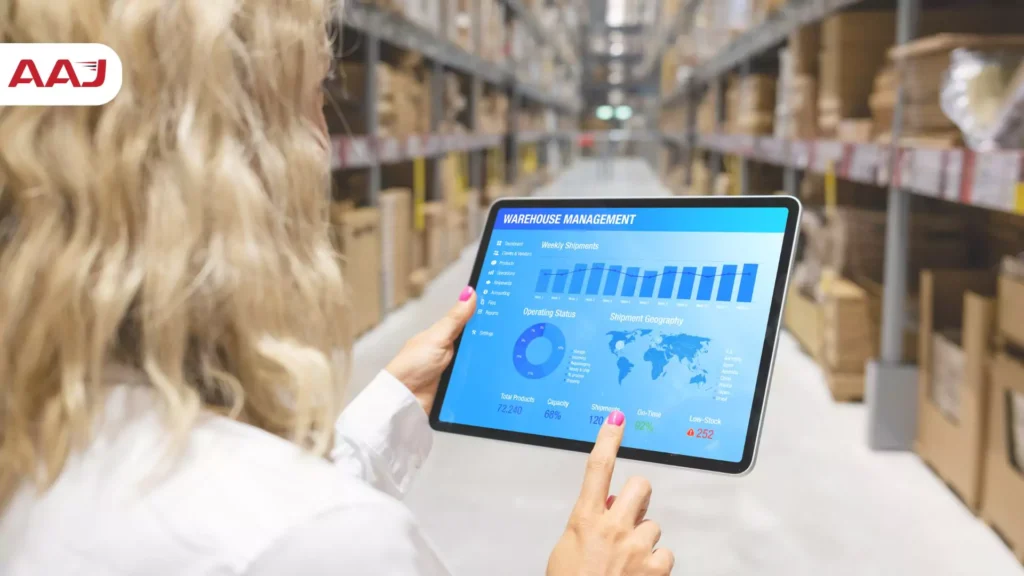
Managing inventory can be tricky, but the right Inventory Management system can make all the tasks easy. Let’s break down the four main types of inventory management that logistics companies commonly use:
1. Manual Inventory System
This old-school method involves physically counting every item and logging it on paper. While it’s simple and requires no fancy tech, it’s time-consuming and prone to errors. Imagine trying to keep track of thousands of items this way—one misplaced tally mark, and your inventory could be off by a mile! It’s best suited for small businesses with limited stock.
2. Periodic Inventory System
With the Periodic Inventory System, companies only count their stock at set intervals, like monthly, quarterly, or even yearly. This method doesn’t track inventory in real time, so it works better for businesses that don’t need constant updates. Think of it like checking in with your stock once in a while instead of keeping tabs on it 24/7. It’s simple but can leave gaps in data if you’re not careful.
3. Just In Time
For those who love efficiency, the Just In Time (JIT) warehouse and inventory management system is all about keeping minimal stock on hand. Companies only order what they need when they need it, which saves on storage costs and reduces excess inventory. It’s like having a fridge that never runs out of food because you order groceries right before you cook. However, JIT relies heavily on smooth supply chains—any disruption, and you’re left with nothing to sell.
4. ABC Inventory
The ABC Inventory System takes a more strategic approach by categorizing goods into three classes:
- Class A (high-value items that require close monitoring)
- Class B (moderately valuable items)
- Class C (low-value items that don’t need much attention)
This method helps businesses focus their resources where it matters most, ensuring that the most valuable products get the attention they deserve. At the same time, less important items are managed with a lighter touch.
Process Of Warehouse Inventory Management
The Warehouse inventory management system involves the following processes, which are listed below:
1. Receiving: Whenever goods are delivered to the warehouse, they are checked properly. Some of the main features are checked, like their quality, quantity and accuracy.
2. Storage: Whenever the goods are received, they are stored in their specific locations inside the warehouse logistics. Efficient, good storage will ensure maximum storage space inside the warehouse.
3. Inventory Tracking: Different methods like barcode scanners or RFID tags monitor the stock levels.
4. Picking: Whenever a customer places an order, the particular good is picked from its location.
5. Packaging: The workers of the warehouse package the particular goods.
6. Shipping: The packed item is sent out for delivery.
Why is Warehouse and Inventory Management Important for Business?
1. Space Utilization
The warehouse management system organizes the storage spaces effectively. It maximizes space inside the warehouse storage area. The WMS involves strategies like slotting, where frequently used goods are stored in easily accessible places, and less frequently used goods are stored in far places.
2. Cost Control
Poor warehouse and inventory management can lead to overstocking of goods and products, which can further lead to higher warehousing costs. It holds goods inside the warehouse unnecessarily. Similarly, understocking of goods cannot fulfill customer demand immediately, which can directly affect a business sale. Efficient inventory management will help to order the right quantity of products and avoid both overstocking and understocking of goods.
3. Enhance Customer Satisfaction
Whenever a customer places an order and the product is not in stock, then it delays the delivery, which has a negative impression on the customer. So it’s quite essential to track inventories and replenish if required so that out-of-stock problems can be avoided. Ecommerce fulfillment at the right time helps increase customer satisfaction.
4. Reduces Wastage
Whenever products are stored on a shelf for a longer time, they get outdated. Proper inventory management systems like first in and first out ensure that older goods are first delivered to the customers and then new stock is added in the warehouse.
Difference Between Warehouse And Inventory Management
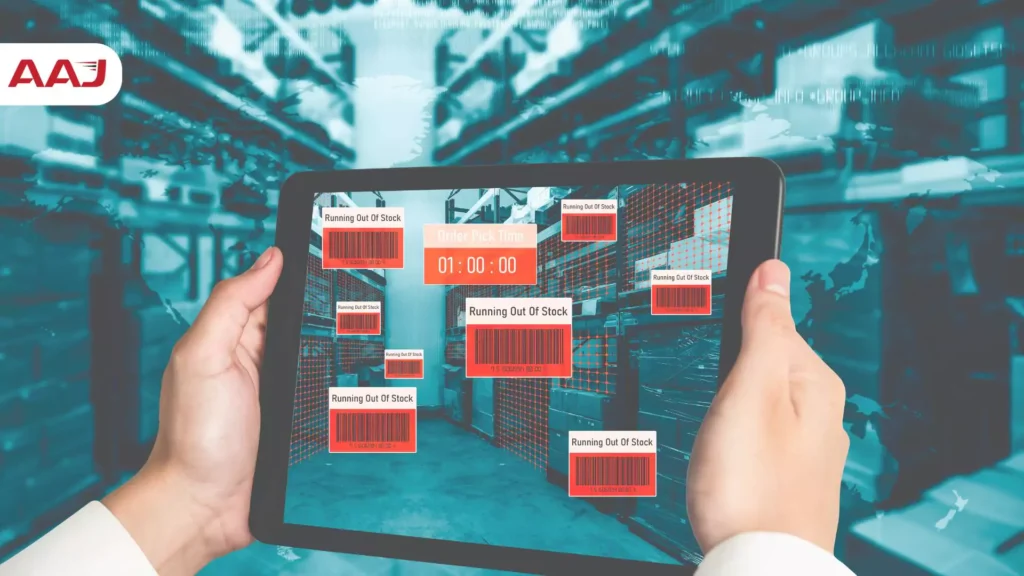
1. Warehouse management involves processes like receiving goods, storing them, packaging and then shipping them.
Inventory management focuses on stock levels and ensures the right quantity of product should be there in the warehouse.
2. The main goal of the warehouse management system is to store goods inside the warehouse in such a way that it maximizes space and improves workflow.
The main goal of the inventory management system is to maintain the right amount of stock and avoid overstocking and understocking.
Advantages And Benefits Of Implementing Inventory and Warehouse Management
1. Improves Efficiency
Optimizing warehouse and inventory management will help to reduce manual labor and speed up the supply chain processes in a company. It even reduces errors and minimizes delays.
2. Space Utility
The warehouse management system organizes goods systematically so that maximum space inside the warehouse can be utilized.
3. Reduces Costs
Poper warehouse inventory management avoids overstocking and understocking and thus reduces storage costs.
4. Improves Accuracy Of Inventory Data
Automated inventory tracking can provide real-time data on inventories stored inside the warehouse and their locations.
5. Customer Satisfaction
Proper inventory management can provide goods at the right time to customers, and this helps in increasing customer satisfaction.
6. Reduces Wastage
Warehouse inventory management manages time-sensitive products by using first-in and first-out service. It reduces waste and avoids unnecessary costs for a Company.
Best Practices To Do Warehouse And Inventory Management
1. Use First In And First Out System
Warehouse and inventory management Companies should use the first in and first out system. It means the warehouse partner should sell out the old goods first and then refill the warehouse with new ones.
2. Reduce Manual Input
Manual tasks take a lot of time and have chances of errors. Try to use drones, sensors or RFID tags to track inventory.
3. Forecast Demand Accurately
Use historical data to predict future inventory requirements, and this avoids overstocking and understocking.
4. Train Staff
Train staff on how to use RFID technology or barcode scanners to track inventory accurately.
5. Use The Warehouse Management System
It monitors the entire warehouse and provides real-time data.
Conclusion
Effective warehouse and inventory management is essential for the success of any business. It ensures proper flow of goods from storage to delivery and thus reduces operational costs. Proper management will also avoid overstocking and understocking issues. Proper warehouse and inventory management services can deliver products to customers at the right time and increase customer satisfaction.